XIAOYIN
Laura
WU |
Architectural Engineering
SENIOR THESIS
Lighting/Electrical |
|
FRUANHOFER CSE |
> 5 CHANNEL CENTER STREET, BOSTON, MA |
Progress |
Date |
OWNER PERMISSION OBTAINTED |
Aug 30, 2013 |
CPEP SITE CREATED |
Sep 06, 2013 |
STUDENT BIO POSTED |
Sep 11, 2013 |
BUILDING STAT PART1 POSTED |
Sep 16, 2013 |
TECH REPORT MEMO POSTED |
Sep 16, 2013 |
TECH REPORT 1 POSTED |
Sep 19, 2013 |
BUILDING STAT PAGE FINISHED |
Oct 13, 2013 |
TECH REPORT 2 POSTED |
Oct 15, 2013 |
ABSTRACT POSTED |
Oct 21, 2013 |
TECH REPORT 3A POSTED |
Nov 11, 2013 |
TECH REPORT 3 POSTED |
Dec 06, 2013 |
TECH REPORT 3 REVISED |
Dec 14, 2013 |
PROPOSAL POSTED |
Jan 17, 2013 |
FINAL REPORT POSTED |
Apr 09, 2014 |
FINAL PRESENTATION POSTED |
Apr 14, 2014 |
FINAL REPORT PAGE UPDATED |
Apr 29, 2014 |
CONTACT PAGE CREATED |
Apr 29, 2014 |
REFLECTION PAGE POSTED |
Apr 30, 2014 |
CPEP SITE UPDATE FINISHED |
Apr 30, 2014 |
|
|
|
|
|
|
|
|
|
|
|
|
|
|
|
General Building Data |
|
BUILDING NAME |
|
Fraunhofer CSE |
|
LOCATION |
|
5 Channel Center Street, Boston, MA |
|
OCCUPANCY TYPE |
|
Offices and research laboratories (Group B) and conference room (Group A-3) |
|
SIZE |
|
42150 SF |
|
STORIES ABOVE GRADE |
|
6 |
|
PROJECT TEAMS
|
|
Owner: Fraunhofer USA
General Contractor/Construction Manager: Gilbane Building Co. www.gilbaneco.com
Architects: DiMella Shaffer www.dimellashaffer.com
Structural Engineer: McNamara/Salvia, Inc. www.mcsal.com
MEP/FP/Tel Data Engineer: BR+A Consulting Engineers www.brplusa.com
Lighting Consultant: Lam Partners www.lampartners.com
Plumbing/HVAC Services: Northeastern Mechanical www.northeasternmech.com
Civil Engineer: VHB, Inc. www.vhb.com
Geotechnical Engineer: Haley & Aldrich, Inc. www.haleyaldrich.com |
|
DATES OF CONSTRUCTION |
|
Jan 2012— Apr 2013 |
|
ACTUAL COST INFO |
|
Not clear. This renovation project is designed for Fraunhofer Building Technology Show Case (http://cse.fraunhofer.org/5cc/). For this specialness of the project, almost all the products and materials are donated by manufacturers. Therefore cost is hard to be estimated. |
|
PROJECT DELIVERY METHOD |
|
Base building—Tenant Fit-Up |
Architecture |
|
DESIGN &
FUNCTIONAL COMPONENT
|
|
The project is a renovation for a 100-year old historical building of six-story, three-bay loft brick structure with classical revival-style detailing. The Fort Point Channel district is marked by an exceptional degree of visual uniformity. Fraunhofer Building, one of the buildings in the Fort Point Channel area, is not an exception of a loft structure built in 1913 by the Boston Wharf Company, and represent an unusually coherent and well-preserved collection of late 19th and early 20th century lofts that reflect a critical period of social, economic, and physical development in the City and the region. The loft buildings are generally masonry, with simple volumes and flat roofs. Buildings are elegantly proportioned, with classically inspired details concentrated at entrances and cornices. And the structure is left unchanged in this project to conserve the significant continuity throughout the District in terms of massing, scale, and style.
The majority of the structure has been left almost unchanged since its construction 100 years ago. In planning the renovations, CSE worked closely with the Fort Point Channel Landmark District Commission and National Park Service’s Historic Preservation Planning Program, developing a retrofit plan that could deliver energy savings and still respect the building’s historic character. |
|
APPLICABLE CODES |
|
CODE TYPE |
APPLICALE CODE (Model Code Basis) |
Buliding 780 CMR |
Massachusetts Building code (8th Ed.)
(International Building Code 2009, amended) |
Fire Prevention |
527 CMR: Massachusetts Fire Prevention Regulations |
ADA |
Americans with Disabilities Act (2010 ADAAG), & Title II |
FHA |
Fair housing Act (Safe Harbor: FHA Design Manual) |
Electrical |
527 CMR 12.00: Massachusetts Electrical Code
(2011 National Electrical Code, amended) |
Elevators |
524 CMR: Massachusetts Elevator Code |
Mechanical |
2009 International Mechanical Code |
Plumbing |
248 CMR: Massachusetts Plumbing Code (2005) |
|
|
ZONING |
|
Industrial District—Restricted Manufacturing: Planned Development Area Designation
http://www.bostonredevelopmentauthority.org/zoning/downloadZone.asp |
|
HISTORICAL REQUIREMENT |
|
The Fort Point Channel Landmark District Standards and Criteria (Design Guidelines, 2008)
http://www.cityofboston.gov/landmarks/historic/fpc.asp |
Building Enclosure |
|
FAÇADE |
|
The renovation completely preserves the existing building condition which incorporates brick wall façade. For detail, please refer to the drawing below: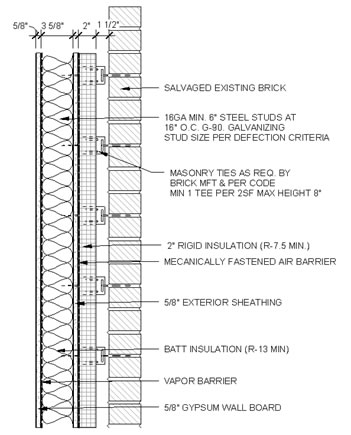 |
|
WINDOW |
|
Windows incorporates solar control glass (manufacture: Guardian) and automated shading control system (manufacturer: Hunter Douglas) |
|
ROOFING |
|
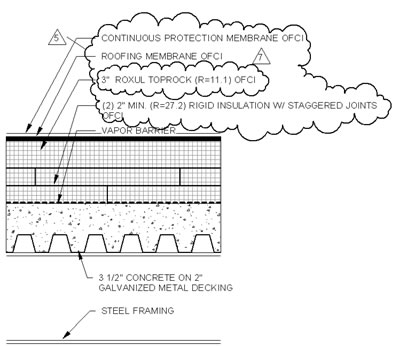 |
Sustainability Features |
|
The Building Technology Showcase is a deep energy retrofit of a historic building, incorporating a variety of energy-efficient systems, materials and measures to create significant reductions in whole-building energy consumption. |
|
ENERGY MANAGEMENT |
|
A building management system (BMS) provided by Siemens can monitor and control all functional components of the Showcase to optimize economy, efficiency, and comfort. Additional support is provided by acontinuous commissioning system from Cimetrics that monitors performance and energy consumption, and then uses this information to identify potential issues or create recommendations for efficiency improvements. |
|
HVAC |
|
The Showcase saves energy by reducing heating and cooling loads and using more energy-efficient HVAC systems. Installed features include:
Chilled beams and radiant chilled panels (Price HVAC)
Displacement ventilation (Price HVAC)
Coof roof membrane (Cooley Group)
Variable frequency drives (Taco, Yaskawa)
Energy-efficient chiller systems (Multistack)
Radiant baseboards (Smiths) |
|
ELEVATOR |
|
The building features a ThyssenKrupp synergy elevator driven by a gearless motor. In addition to being more efficient than a conventional model, regenerative braking technology allows the elevator to generate electricity while in use. |
|
FINISHES |
|
Solar control glass (Guardian)
Automated shading control (Hunter Douglas)
Phase change material insulation (DuPont)
Vacuum insulation panels (VIPs) (Dow Corning)
Formaldehyde-absorbing drywall (CertainTeed)
Sustainable rubber flooring (nora)
Countertops made from recycled glass (Merrimack Stone) |
Primary Engineering System |
|
CONSTRUCTION |
|
This project is a historical building renovation and tenant fit-out. Gilbane Building Co. is the general contractor of this building and is responsible for the construction process of the Fraunhofer CSE building. The whole construction process lasts for over a year from January, 2012 to April, 2013.
Due to the special situation of the particular project, there is hardly an official estimate for the renovation. The almost all the building electrical, lighting and mechanical system as well as building material are donated from different manufacturers for the building technology showcase purpose of the building. The owner cannot provide an estimation number of this construction project. The delivery is not a regular method. It’s a base building--tenant fitup process. |
|
ELECTRICAL |
|
There is a single electrical entry into the building providing power to the main distribution switchboard and the main fire pump. The electrical system of the building has a utilization voltage of 480/227V, 3 phase. Different utilization voltage is used throughout the building due to the variety of equipment needs in the building. The building emergency power system is powered by a 350kW, diesel filled, 480/277V, 3 phase, 4 wire standby emergency generator located on the rooftop. It provides the building with 120V emergency power for lighting and receptacles. There are 3 photovoltaic arrays on the rooftop inverting solar power to electric power for the building. There are pv panels mounted on the roof and west and east façades. |
|
LIGHTING |
|
The lighting design for Fraunhofer CSE building is energy efficient and sophisticated. The building is the project of the Fraunhofer building technology showcase. The lighting system donator provided the project the very up front. Most of the lighting fixture sources are LED and some are fluorescent source. A large amount of color changing LED is used in the building as well for the aesthetic purposes. The lighting systems work on both 277V and 120V system. Dimmable lighting fixtures are widely applied throughout the entire building. The lighting control system is connected to BAS system. Shading system is installed in the building as part of a daylightign control system. |
|
MECHANICAL |
|
There are 2 boilers to reheat/preheat the hot water, 4 pumps for roof hot water service and basement fuel oil supply. There are two air handling units locate on the roof serve for building ventilation and exhaust. They work on 460V, 3 phase motors. The AHU supply air quantity to be 20,000 CFM. And its cooling coil load is based on 100% CFM and the preheat coil load sized for 75% CFM preheat coil sized for 100% outside air at 0⁰F. High efficient active chilled beams are used in the building to supply heating and cooling air. The building also utilizes in-floor radiant heating cooling system on 1st and 3rd floor for additional heating and cooling. 11 water pumps are located on different levels in the building supply for chilled water, condenser water and chilled beam water. |
|
STRUCTURE |
|
The building is a three-bay loft steel frame structure. All columns are the existing steel columns with existing concrete column bases. The typical bay spans as long as 20ft. The main wall structure is masonry, brick wall with metal studs. The floors are existing typical wood decking with glass fiber reinforced concrete on top and the roof is existing wood deck and concrete slab. The building is a 100-year-old historical building so the typical beams sizes are hard to be obtained at the point. |
Additional Engineering & Engineering Support Systems |
|
FIRE PROTECTION |
|
The building is primarily depends on active fire protection system. The building utilizes stand pipe and sprinkler system. There are alarm check valves and manifolded configuration system control and drain valves for pressure in excess of 175PSIG installed in the building providing water pressure for the sprinkler system. All spaces on each floor of the building belong to ordinary hazard group 2. Each sprinkler protects an area of 130ft2 and the hose allowance is of 250GPM. |
|
TRANSPORTATION |
|
The building features energy efficient elevator located at the building west. And there is a handicap chair lift in the lobby can be used for transportation from the lower level lobby to the upper level reception area. |
|
SPECIAL SYSTEMS |
|
The building has a photovoltaic system providing electric power in addition to the regular electric power supply from the area. Other than conventional heating/cooling mechanical system the building also has in-floor radiant heating/cooling systems on 1st and 3rd floor. |
|
Note: While great efforts have been taken to provide accurate and complete information on the pages of CPEP, please be aware that the information contained herewith is considered a work‐in‐progress for this thesis project. Modifications and changes related to the original building designs and construction methodologies for this senior thesis project are solely the interpretation of Xiaoyin (Laura) Wu. Changes and discrepancies in no way imply that the original design contained errors or was flawed. Differing assumptions, code references, requirements, and methodologies have been incorporated into this thesis project; therefore, investigation results may vary from the original design. |
|
This page is last updated on Sep 30, 2013 By Xiaoyin Wu and is hosted vby the AE Department ©2013. |
|